HTWK-Forschungsgruppe FLEX präsentiert durchgängig digitales Design- und Fertigungskonzept für ressourceneffiziente Fassaden- und Dachkonstruktionen
Ob Spinnennetze, Bienenwaben oder Insektenflügel – die Natur zeigt uns, wie durch Netzstrukturen mit minimalem Materialeinsatz leistungsstarke Strukturen entstehen. Diese Erkenntnis setzt die Forschungsgruppe FLEX der Hochschule für Technik, Wirtschaft und Kultur Leipzig (HTWK Leipzig) nun im InNoFa-Projekt (Individual Node Facade) um: Ein netzartiges Geflecht aus standardisierten Stäben ist durch individuell geformte, 3D-gedruckte Knotenpunkte verbunden und sorgt für maximale Stabilität bei minimalen Ressourceneinsatz. So entstehen organisch geformte Stabnetzwerke für Fassaden, Dächer, Brücken oder Masten. Einen zwei mal drei Meter großen Ausschnitt einer so konstruierten Glasfassade stellen die Forschenden vom 17. bis 19. Mai 2022 auf der Rapidtech-3D-Druck-Messe aus.
Fassadenkonstruktion aus dem 3D-Drucker
Im Bausektor müssen Ressourceneffizienz und Ästhetik oft zurückstehen, um durch Standardisierung Arbeitskosten zu sparen. Die Forschungsgruppe FLEX möchte diesen Widerspruch auflösen, indem sie Konstruktion und Fertigung mithilfe digitaler Prozesse und 3D-Druck vereint. Sie hat eine durchgängig automatisierte und digitale Prozesskette für geometrisch individuelle Knotenelemente entwickelt, die standardisierte Stäbe zu einem Tragwerkskonstruktion verbinden. Gefertigt werden die Knoten per 3D-Druck – derzeit aus Aluminium, aber perspektivisch aus Stahl. „Mit dem InNoFa-Modell zeigen wir beispielhaft, wie sich Ästhetik und Ressourceneffizienz vereinen lassen, wenn automatisierte Fertigung bereits in der Konstruktionsphase mitgedacht wird“, so Prof. Alexander Stahr von der Forschungsgruppe FLEX. „Im Moment müssen selbst regelmäßig geformte Stabnetzwerk-Konstruktionen, wie wir sie beispielsweise als Dach im Leipziger Fußballstadion vorfinden, komplett in Handarbeit zusammengefügt werden“, erklärt der Professor für Tragwerkslehre weiter. Das heißt, die Stäbe werden einzeln mit den Knoten verschweißt – ein enormer Arbeitsaufwand. Stahr: „Durch Automatisierung und generative Fertigungsverfahren können wir Material, Zeit und Arbeitskraft sparen – und gleichzeitig individuelle Geometrien verwirklichen.“ Die Stabverbindungen müssen also nicht per Handarbeit gefertigt werden, sondern können dank digitaler Prozessketten passgenau gedruckt werden.
Prototyp vor Ort anschauen
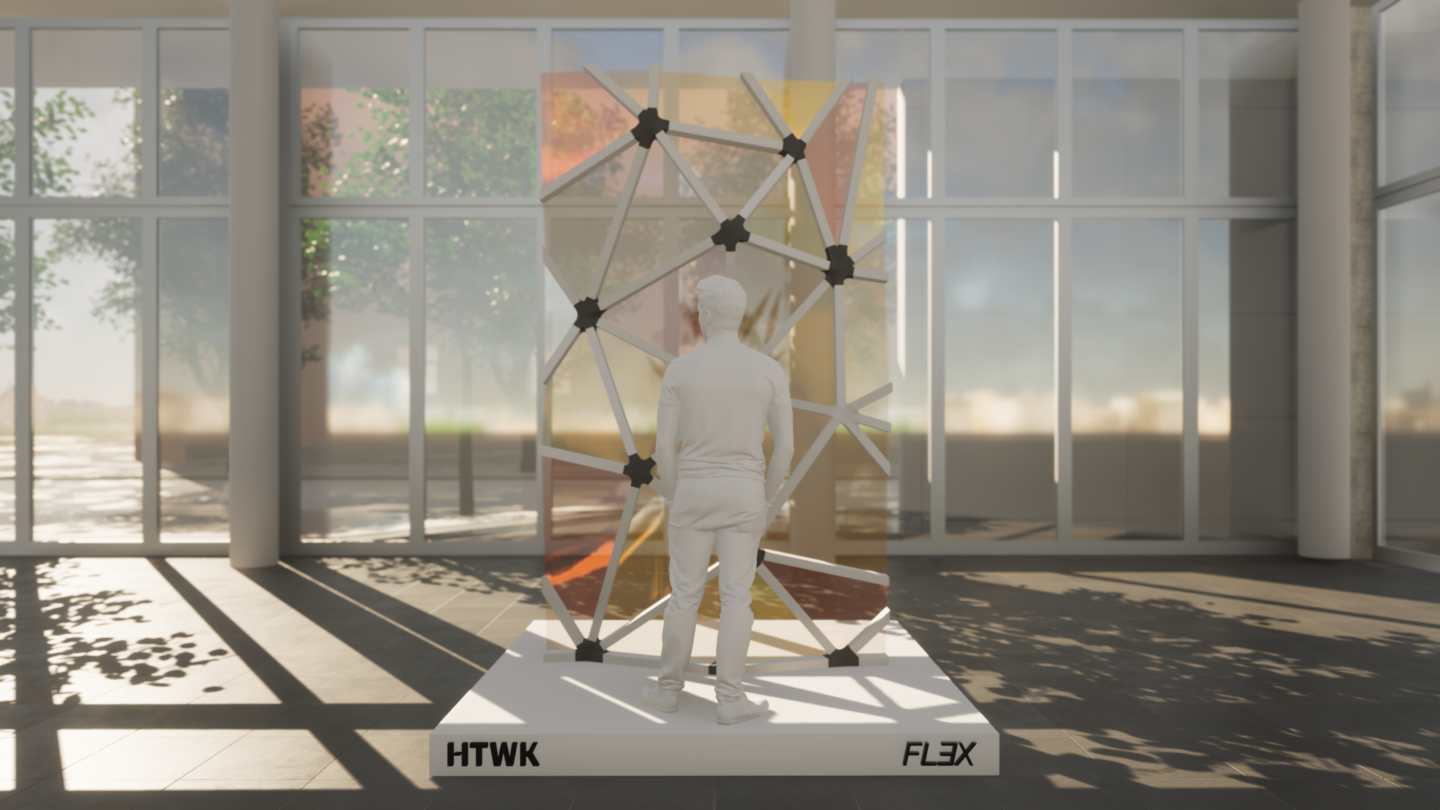
Interessierte, die sich das prototypische Fassaden-Modell ansehen und mit den Forschenden von FLEX ins Gespräch kommen wollen, finden den Stand der HTWK Leipzig auf der Rapidtech-Messe an der Standnummer 2-622. Direkt daneben hat die Hochschule Mittweida ihren Ausstellungsstand. Diese hat die Metallknoten aus dem 3D-Drucker für InNoFa hergestellt. Eine weitere Gelegenheit zur Besichtigung des Demonstrators bietet sich beim Leipziger Fassadentag am 20. September 2022.
Hintergrund zu FLEX
Die Forschungsgruppe FLEX an der HTWK Leipzig ist ein interdisziplinäres Team aus den Bereichen Architektur, Bau- und Wirtschaftsingenieurwesen. Unter Leitung von Prof. Alexander Stahr widmet sich die Forschungsgruppe der digitalen Verknüpfung von Planungs- und Ausführungsprozessen – mit dem Ziel, Ressourcen in Architektur und Bautechnik effizienter zu nutzen. Dabei entstehen digitale Werkzeuge für materialeffiziente, gekrümmte Konstruktionen mit individueller Geometrie. Die Forschungsgruppe ist Mitglied im Transferverbund Saxony⁵ der fünf sächsischen Hochschulen für Angewandte Wissenschaften und realisiert dort Forschungs- und Entwicklungsprojekte in den Bereichen 3D-Druck, Holzbau und parametrisches Design.
Autorin: Dr. Rebecca Schweier