Oktober 2021 | Vibrationssensoren übermitteln via RF-Technologie Echtzeit-Analysedaten für die Schwingungsdiagnose der Wälzlager im Getriebe riesiger Schaufelradbagger
Die Wartung rotierender Getriebe in Großmaschinen ist zeitaufwändig, kostenintensiv und sehr komplex. Ein Getriebeverschleiß bei Großmaschinen wie Schaufelradbaggern, Tunnelbohrern, Zementmischern oder Windrädern führt zu hohen Wartungskosten und im schlimmsten Fall zum Komplettausfall der Maschine.
Im Rahmen des Forschungsprojektes „MIBRAG“ hat das Team von Prof. Dr.-Ing. Faouzi Derbel Fakultät Ingenieurwissenschaften HTWK Leipzig in Kooperation mit der Mitteldeutschen Braunkohlengesellschaft mbH (MIBRAG) seit 2016 drahtlose Sensorsysteme entwickelt, die eine technische Zustandsdiagnostik der Wälzlager der Planetengetriebe in Großmaschinen ermöglicht.
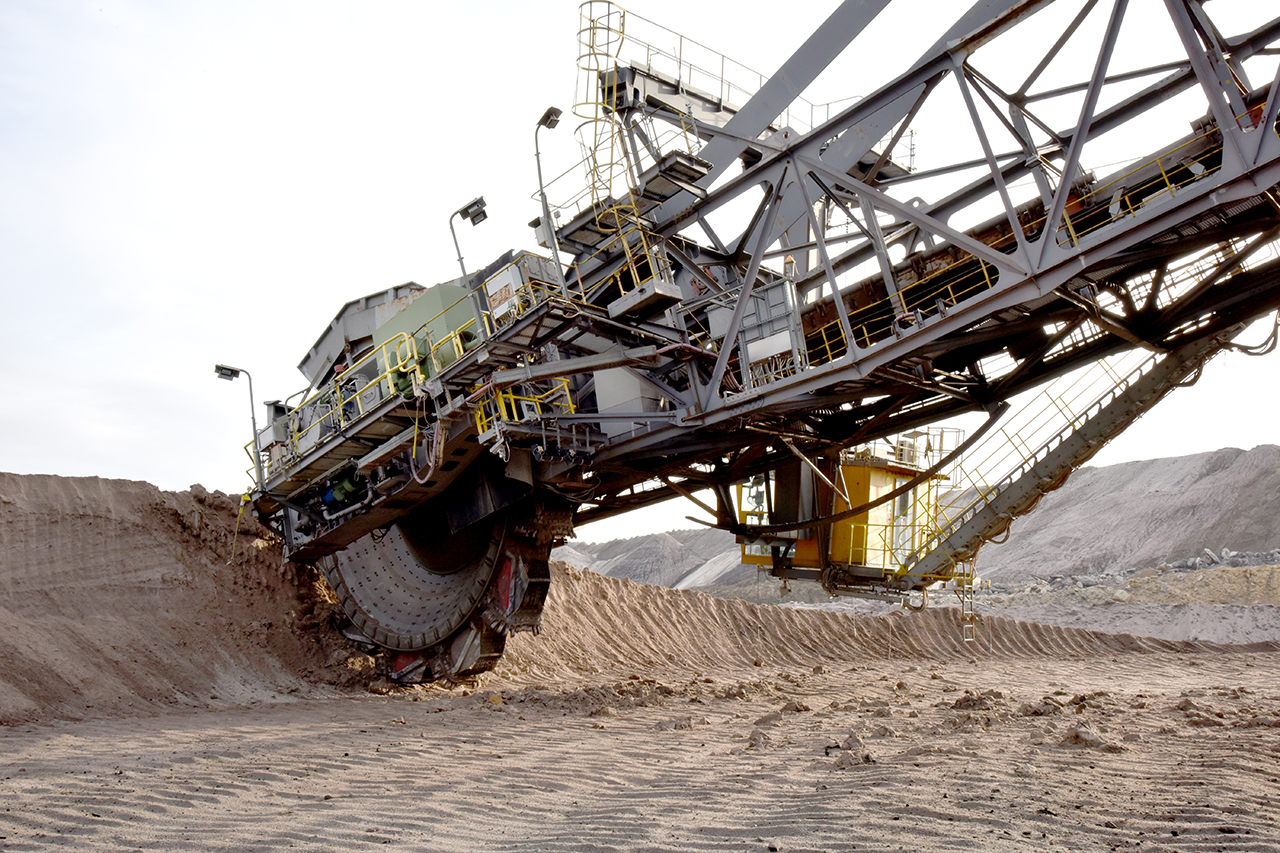
Getriebe-Zustandsdiagnose jetzt live und digital
Seit 5. Oktober 2021 ist die neueste Generation der im Projekt entwickelten MIBRAG-Module im Einsatz. Die Funk-Sensor-Hardware sendet täglich und live Vibrationsdaten aus dem Inneren des Großgetriebes eines Schaufelradbaggers. Ausgewertet werden diese Daten mittels unterschiedlicher mathematischer Methoden, die eine Prognose der Ausfallwahrscheinlichkeit in Abhängigkeit des diagnostizierten Zustandes berechnet und Handlungsempfehlungen für anstehende Wartungsarbeiten benennt.
Der Entwicklungsprozess der MIBRAG-Module
Die Wälzlager der Planetengetriebe wurden in der Vergangenheit punktuell gewartet: Alle vier Wochen wurden schwingungstechnische Messungen nach DIN-Norm vorgenommen, indem außerhalb der Getriebe Schwingungssensoren angebracht wurden. Aufgrund der Komplexität und Größe der Planetengetriebe konnten dabei nicht alle Verschleißvorgänge erfasst werden. Aus ökologischen und ökonomischen Gesichtspunkten Bedarf es einer exakteren und vor allem regelmäßigeren technischen Diagnostik der Getriebe.
Für die Entwicklung eines Sensorsystems, dass im Innern der Getriebe eingebaut werden sollte und eine regelmäßige digitale Messung des Verschleißzustandes ermöglicht, beauftragte die MIBRAG dann 2016 das Team von Prof. Dr.-Ing. Faouzi Derbel von der Fakultät Ingenieurwissenschaften der HTWK Leipzig.
„Eine große Herausforderung stellten bei der Entwicklung der neuen MIBRAG-Module die Getriebe- und Lager-Analysen dar, da die benötigten Vibrationssensoren möglichst in das Innere eingebracht und die Messwerte kabellos nach Außen übertragen werden müssen. Der Kompromiss zwischen Abtastrate und Energiebedarf ist nur eines von vielen spannenden Forschungsthemen, die wir in den letzten Jahren lösen mussten“, betont Projektmitarbeiter Florian Strakosch.
_Data-Transfer durch Ölgetriebe
Florian Strakosch arbeitet bereits seit der ersten Stunde mit am Forschungsprojekt „MIBRAG“ und befasste sich unter anderem mit der Datenübertragung. Damit Sensoren, die im Innern der Getriebe angebracht sind, ihre Messergebnisse auch durch das Öl hindurch per Funk senden können, musste die Datenübertragung erst einmal erforscht werden.
Ihre Forschungsergebnisse zur Ausbreitung elektromagnetischer Wellen in Öl veröffentlichen Prof. Derbel und Florian Strakosch im Artikel „Investigation of Radio Propagation in Moving Gear Oils“. Auf der „15. Multi-Conference on Systems, Signals and Devices“ (SSD) erhielten Strakosch und Prof. Derbel 2018 den „Best Paper Award“ und erlangten internationale Anerkennung für ihre Forschungsarbeit.
_Extrembedingungen
Das Wissenschaftsteam von Prof. Derbel musste unterschiedliche Herausforderungen bei der Entwicklung der Funksensoren meistern. Es galt Sensoren zu entwickeln, die autonom Messdaten erheben und per Funk durch Öl und Metall an Empfänger außerhalb des Getriebes senden können und wenig Energie benötigen, d. h. ohne Batteriewechsel lange arbeiten müssen, und die den Extrembedingungen im Innern des Getriebes standhalten.
Denn im Inneren der Planetengetriebe ist der untere Teil zur Kühlung des Getriebes mit Öl gefüllt, welches sich auf bis zu 95 Grad Celsius aufheizen kann. Die einzelnen Zahnräder des Planetengetriebes tauchen in dieses Ölbad rotierend ein und wieder aus. Die zu entwickelnden Sensoren inklusive der Batterie für die Stromversorgung müssen daher im heißen Öl und auch in der Luft zuverlässig funktionieren können. Im Winter kann die Luft im oberen Bereich darüber hinaus Minusgrade haben, sodass die Sensor-Hardware auch extreme Temperaturspannen überstehen muss.
_5-Cent-große MIBRAG-Module
Für die Platzierung der gesamten Sensortechnik identifizierte das Wissenschaftsteam die Zentrierbohrungen der Getriebe, mit denen die Zahnräder bei Wartungsarbeiten ausgerichtet werden. Das begrenzt die Maße für die gesamte Technik auf die Größe einer Zentrierschraube.
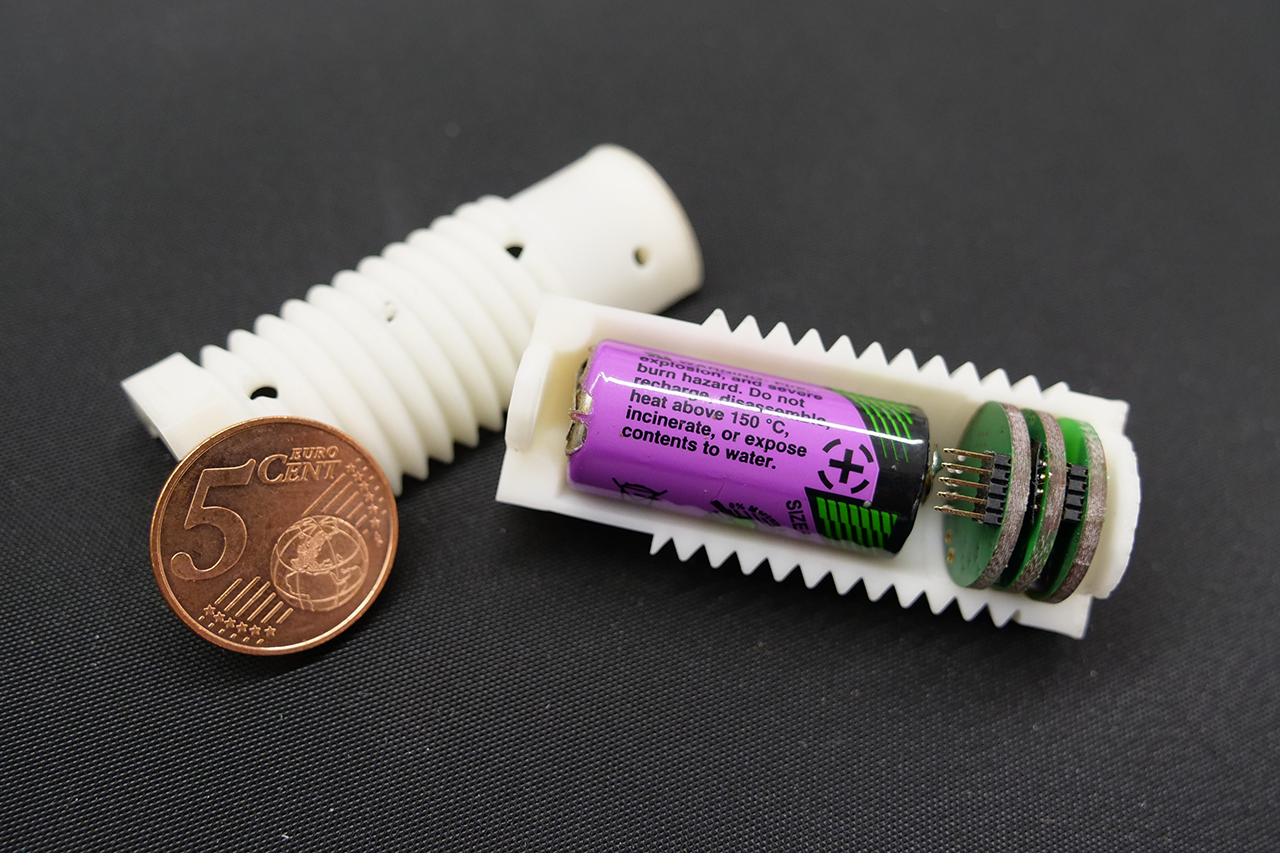
Das Team entwickelte 5-Cent große MIBRAG-Module, die aus mehrachsigen Beschleunigungssensoren, einer Temperatur-Messung, einem Mikrokontroller, einem Funk-Chip mit zugehöriger Antenne, und einer Batterie bestehen. Alle Komponenten werden in eine hohle Schraube, die mit 3D-Drucker gefertigt wird, gesetzt, und ermöglichen mehrere Jahre lange eine dauerhafte, zuverlässige Getriebediagnose.
Seit 2019 erprobt das Team der HTWK Leipzig die MIBRAG-Module im Langzeiteinsatz und optimiert einzelne Komponenten stets weiter. Für Die Datenauswertung wurde eine eigene Software entwickelt, die die erhobenen Messdaten des Sensors automatisch auswertet und Fehlzustände erkennt. Dafür wertete Projektmitarbeiter Florian Strakosch über viele Jahre Excel-Listen mit Messwerten aus, die in diversen Praxistests erhoben wurden.
„Ziel ist es, automatisch aus den Messungen den Verschleiß des Getriebes abzulesen. Dazu habe ich unsere Daten mit den Betriebszuständen des Baggers und den Ergebnissen der konventionellen Getriebediagnosen nach DIN-Norm abgeglichen. Anschließend habe ich geprüft, welche Daten relevant sind, sodass wir die Häufigkeit und die Detailtiefe der Messungen so weit reduzieren konnten, dass die Batterie mehrere Jahre lang halten kann“, erläutert Projektmitarbeiter Florian Strakosch.
Am 5. Oktober 2021 wurde erfolgreich die neueste Generation der Funk-Sensor-Hardware im Planetengetriebe des Schaufelradbaggers 1553 im Tagebau Profen in Betrieb genommen.
Einsatzmöglichkeiten
Die MIBRAG-Module wurden für die Zustandsdiagnose ölgekühlter Planetengetriebe von Tagebaugroßgeräten entwickelt, der Einsatzbereich der Funk-Sensor-Module kann jedoch auf alle Planetengetriebe erweitert werden und beispielsweise den Getriebeverschleiß von Windrädern, Zementfabriken und riesigen Tunnelbohrern diagnostizieren.